Activated carbon adsorption+CO catalytic combustion is a highly respected waste gas purification technology in the current environmental protection industry. It combines the adsorption and desorption characteristics of activated carbon and the low-temperature energy-saving characteristics of catalytic combustion. When treating mixed waste gases with different concentrations and components, it can easily meet the emission standards stipulated by the environmental protection department. Therefore, it is highly praised and has broad prospects.

2. [Adsorption Concentration+CO Catalytic Combustion] Process Principle
Organic exhaust gas enters the activated carbon adsorption chamber under the action of induced draft fan. Because activated carbon has many microporous, large specific surface area and strong adsorption capacity, organic exhaust gas is adsorbed in the microporous of activated carbon, and clean air is discharged at this time.
After a period of time, the activated carbon saturates and stops adsorbing. At this time, the organic waste gas is concentrated in the activated carbon adsorption layer. Then we use catalytic combustion technology to desorb and regenerate the saturated activated carbon and put it back into use.
The organic waste gas with high concentration, low air volume and high temperature desorbed by activated carbon filters into a special plate heat exchanger and exchanges energy with the high temperature gas after catalytic reaction. At this time, the temperature of the exhaust gas source is raised for the first time, and then the gas with a certain temperature enters the preheater for the second time.
In the first stage of catalytic reaction, the organic waste gas is partially decomposed at low temperature, and the energy is released. The waste gas source is directly heated to raise the temperature to the optimum temperature of catalytic reaction.
After a period of time, the activated carbon saturates and stops adsorbing. At this time, the organic waste gas is concentrated in the activated carbon adsorption layer. Then we use catalytic combustion technology to desorb and regenerate the saturated activated carbon and put it back into use.
The organic waste gas with high concentration, low air volume and high temperature desorbed by activated carbon filters into a special plate heat exchanger and exchanges energy with the high temperature gas after catalytic reaction. At this time, the temperature of the exhaust gas source is raised for the first time, and then the gas with a certain temperature enters the preheater for the second time.
In the first stage of catalytic reaction, the organic waste gas is partially decomposed at low temperature, and the energy is released. The waste gas source is directly heated to raise the temperature to the optimum temperature of catalytic reaction.

Only after the temperature detection system meets the temperature requirement of the catalytic reaction can it enter the catalytic combustion chamber. The organic waste gas is thoroughly decomposed in the reaction process, and a large amount of heat is released at the same time. The purified gas converts heat energy to cold air through a heat exchanger, and the clean gas is exhausted by an induced draft fan.
Organic matter maintains spontaneous combustion by using the heat released from oxidation combustion. If the concentration of desorbed exhaust gas is high enough and CO does not need electric power heating under normal conditions, it can achieve real energy saving and environmental protection. At the same time, the whole device is safe, reliable and no secondary pollution.
Organic matter maintains spontaneous combustion by using the heat released from oxidation combustion. If the concentration of desorbed exhaust gas is high enough and CO does not need electric power heating under normal conditions, it can achieve real energy saving and environmental protection. At the same time, the whole device is safe, reliable and no secondary pollution.
3.3. Scope of Application of Adsorption Concentration+CO Catalytic Combustion
The combined process of adsorptive concentration and RCO catalytic combustion can be used to treat organic waste gases produced in various industrial fields such as painting, printing, electromechanical, household appliances, shoemaking, plastics, chemical workshop, etc.
Direct combustion, catalytic combustion and adsorptive desorption should not be used to recover organic waste gases with concentration ranging from 50 ppm to 1000 ppm. In the field of exhaust gas purification with large air volume, the combined process equipment of adsorption concentration and RCO catalytic combustion can make enterprises obtain satisfactory economic and environmental benefits.
Direct combustion, catalytic combustion and adsorptive desorption should not be used to recover organic waste gases with concentration ranging from 50 ppm to 1000 ppm. In the field of exhaust gas purification with large air volume, the combined process equipment of adsorption concentration and RCO catalytic combustion can make enterprises obtain satisfactory economic and environmental benefits.
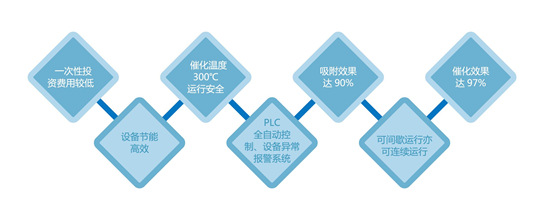
4. Characteristic of [Adsorption Concentration+RCO Catalytic Combustion] System
1. The equipment has advanced principle, unique material, stable performance, simple operation, safety and reliability, energy saving and labor saving, no secondary pollution, small occupation area and light weight. The adsorption bed adopts drawer structure, which is convenient for filling and replacement.
2. Compared with granular activated carbon, honeycomb activated carbon, a new type of activated carbon adsorption material, has superior dynamic performance and is very suitable for use in high air volume.
3. Noble metal catalysts supported by honeycomb ceramics are used in the catalytic combustion chamber with low resistance and high activity. When the concentration of organic waste gas is above 2000 ppm, it can maintain spontaneous combustion.
4. Low power consumption. Because of the small resistance of the bed, low-pressure fan can be used. It not only consumes less power but also has low noise. The power of exhaust fan is shown in the attached table.
5. When catalytic combustion occurs, it needs electric heating to start. After the start of catalytic combustion, the combustion heat energy of organic compounds can be enough to maintain the temperature required for the reaction. At this time, the electric heating stops by itself. The starting time of electric heating is about one hour. The power required for starting is shown in the attached table.
6. Activated carbon bed adsorbing organic waste gas, desorption and regeneration with catalytic combustion waste gas, desorbed gas is sent to catalytic combustion chamber for purification, no external energy is needed, operation cost is low, and energy saving effect is remarkable.
2. Compared with granular activated carbon, honeycomb activated carbon, a new type of activated carbon adsorption material, has superior dynamic performance and is very suitable for use in high air volume.
3. Noble metal catalysts supported by honeycomb ceramics are used in the catalytic combustion chamber with low resistance and high activity. When the concentration of organic waste gas is above 2000 ppm, it can maintain spontaneous combustion.
4. Low power consumption. Because of the small resistance of the bed, low-pressure fan can be used. It not only consumes less power but also has low noise. The power of exhaust fan is shown in the attached table.
5. When catalytic combustion occurs, it needs electric heating to start. After the start of catalytic combustion, the combustion heat energy of organic compounds can be enough to maintain the temperature required for the reaction. At this time, the electric heating stops by itself. The starting time of electric heating is about one hour. The power required for starting is shown in the attached table.
6. Activated carbon bed adsorbing organic waste gas, desorption and regeneration with catalytic combustion waste gas, desorbed gas is sent to catalytic combustion chamber for purification, no external energy is needed, operation cost is low, and energy saving effect is remarkable.
5. Equipment-related parameters
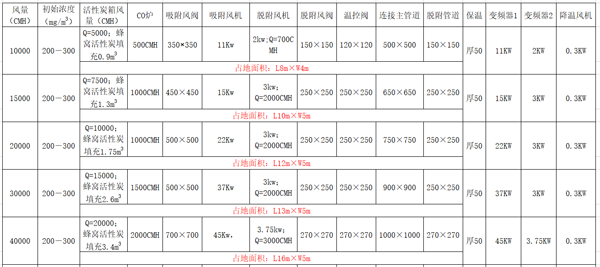
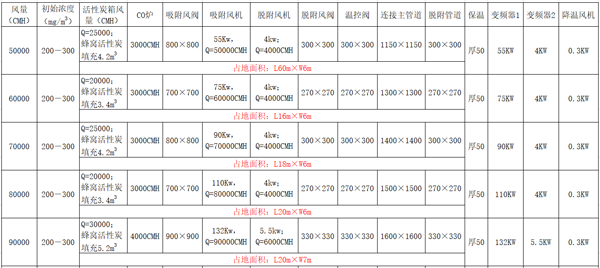
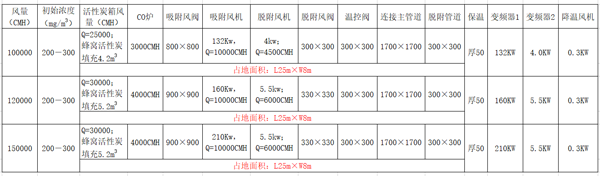